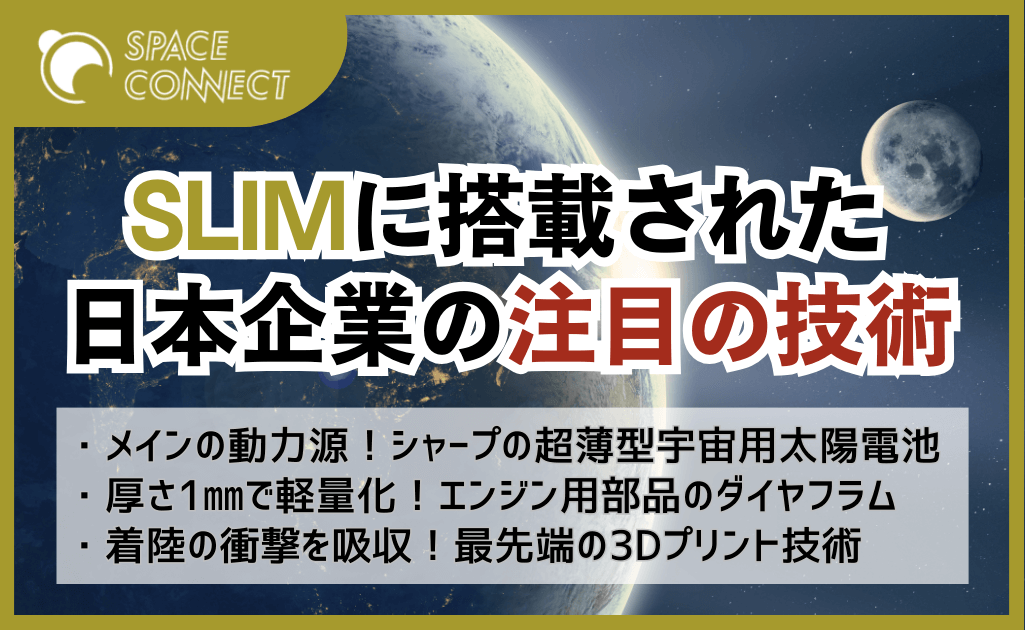
2024年1月20日にJAXAの宇宙科学研究所が開発した小型月着陸実証機「SLIM」が日本初となる月面着陸に成功した。
史上初となる「ピンポイント着陸」では従来の100倍以上の精度である着陸精度10m以内を達成。月探査も実施しており、ほとんどのミッションに成功した。
そんなSLIMが今回の成功に至った背景には、多くの日本の民間企業の技術がある。
本記事では、それらの民間技術の中から3つピックアップしてご紹介します。
SLIMのメインの動力源!「宇宙用太陽電池」
SLIMの電力は搭載されている太陽電池による発電と使い捨て型バッテリーの充電により賄われている。
SLIMは月面着陸時に太陽電池が日の当たらない方向を向き、バッテリーの充電もなくなったことから一時は電源オフ状態となったが、太陽電池に日が当たると電池が正常に再稼働し、SLIMの運用が再開し話題となった。
この太陽電池を開発したのが、日本の大手電子機器メーカーのシャープ株式会社である。
同社は、1967年より宇宙用太陽電池の開発に着手しており、1976年に実用衛星「うめ」に初搭載。
以降、JAXAの認定を受けた国内唯一の太陽電池メーカーとして、約半世紀にわたり宇宙用太陽電池の開発、製造に取り組んでおり、これまでに同社の太陽電池を搭載した人工衛星は約190基にのぼる。
「SLIM」に搭載している薄膜状の宇宙用太陽電池は、2022年に当時世界最高(※1)の変換効率32.65%を達成した太陽電池と同様の技術で開発。
薄いフィルムで太陽電池セルを封止した構造で、1枚のシートあたり縦297㎜×横271㎜である。A4サイズが縦297㎜×横210㎜なので、縦向きのA4のものを横に6㎝程伸ばした大きさだ。
厚さは0.25㎜で質量は約41gと薄くて軽量で、曲面への搭載も可能で、高効率化と軽量化が求められる宇宙用途に適した仕様を実現している。SLIMには26シート搭載されており、合計でも約1.07㎏となっている。
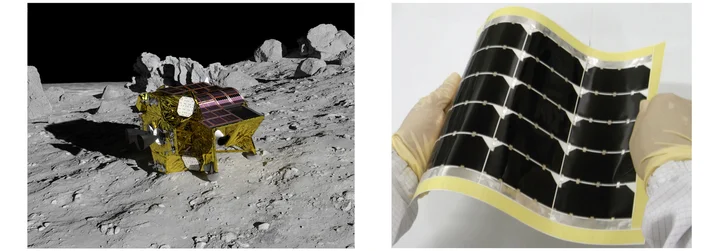
※1:2022年6月6日時点、研究レベルにおける太陽電池モジュールにおいて(シャープ調べ)
厚さ1㎜以下で軽量化!エンジン用部品「ダイヤフラム」
中興化成工業は、エンジンを燃焼させるための酸化剤を貯蔵するタンクの、ポンプの機械部分と送る液体を隔てる弾性の薄い膜「ダイヤフラム」を開発。
ダイヤフラムの酸化剤と逆側にはヘリウムガスが充満しており、このヘリウムガスを加圧することでダイヤフラムを介してエンジンにタンク内の酸化剤の量を送り込むことができる。
一般的には金属やゴム製のダイヤフラムが多く、JAXAの小惑星探査機「はやぶさ」もステンレス製のものであったが、重量や運用性の面で課題があった。
そのため、同社は「柔軟性と軽量性」があり、エンジンに使用される薬液が触れても劣化しにくい「耐薬品性」の特徴をもつ「ふっ素樹脂」を選定。
ふっ素樹脂は一般的な樹脂よりも耐薬品性、耐熱性、耐候性、滑り性などの様々な特性を併せ持つ高機能プラスチックで、同社は1963年の創業時からふっ素樹脂製品を製造している。
東京ドームや高輪ゲートウェイ駅の屋根膜材などに採用されているふっ素樹脂屋根膜材分野で国内唯一の製造メーカーで、世界では3社しかない企業の1つだ。
宇宙業界では、同社が製造した他のふっ素樹脂製品はH2ロケットやH3ロケットのエンジンの部品としても採用されている。
SLIMに搭載されたふっ素樹脂製ダイヤフラムは2014年に開発がスタート。
ふっ素樹脂は変形しやすい素材のため高精度の切削加工が難しいことに加え、薄さが変わることでダイヤフラムの動きにも影響が出るため、要求される動きや加工精度の実現に苦労したという。
しかし、これまで培った加工技術を応用し、加工時の固定方法を工夫することで約1㎜以下の薄肉化に成功した。

着陸の衝撃を吸収!「最先端の3Dプリント技術」
自動車や医療部品関連の金属製品の製造販売を行う株式会社コイワイと、金属3Dプリンターを専門として試作から製品化、量産化までの一貫したサービスを提供する日本積層造形株式会社(JAMPT)は、SLIMの着陸脚先端の衝撃吸収材に最先端の3Dプリント技術を提供。
着陸脚の衝撃吸収材は着陸時の衝撃を低減させるもので、SLIMの場合は直径18㎝の半球状で立体的に網目を巡らした構造をしている。
月面着陸時には自らがつぶれることで、SLIMを着陸の衝撃から守るのに不可欠な役割を果たすのだ。この衝撃吸収材は、JAXAの依頼で始めた共同研究で完成するまでに3年を費やしたそうで、試作品の数は数十から数百になるという。
また、素材はアルミニウムで軽く、重さは400g。様々な方向からの衝撃を等しく吸収することができるとのことだ。
さいごに
いかがでしたか。
SLIMプロジェクトにおける民間企業の協力は、宇宙探査技術の進化において非常に重要な役割を果たしている。
今回紹介した企業の他にも、ピンポイント着陸のソフトをハードウェアに実装する技術を開発したIT企業のソリトンシステムズなど、幅広い業界の高い技術がSLIMに採用されている。
宇宙業界は、多種多様な業界からの知識と技術が融合する場で、自動車、航空、情報技術、材料科学、ロボティクス、さらには3Dプリンティングなど、異なる分野の専門知識が宇宙ミッションの成功に不可欠だ。
これらの技術が集まることによって、日本の宇宙産業は支えられているのだろう。
参考
シャープ製薄膜化合物太陽電池を搭載したJAXAの小型実証機「SLIM(※1)」が月面への「高精度着陸」に成功
長崎県松浦市から、宇宙へ!JAXAの月探査機「SLIM」に約1mm以下の薄肉のふっ素樹脂製「ダイヤフラム」が搭載!